L’ANALISI PREDITTIVA NELLA MANUTENZIONE DEGLI IMPIANTI
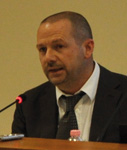
In un momento in cui le aziende manifatturiere del nostro paese sono penalizzate sia da margini operativi in continua riduzione sia da ulteriori oneri fiscali e burocratici che finiscono per ridurre, anziché aumentare, le risorse da dedicare allo sviluppo e all’innovazione, è diventata una priorità eliminare gli sprechi e i costi legati a inefficienze e fermo impianti. Da vent’anni, la Rancan Elettrotecnica, che annovera fra i suoi clienti alcuni dei maggiori gruppi industriali del Nordest, e non solo, interviene nella manutenzione di diverse tipologie di macchine elettriche rotanti come alternatori, motori asincroni, motori a corrente continua e convertitori di frequenza. Considerando che, in questa difficile congiuntura economica, c’è la tendenza a ridurre o rinviare il servizio di manutenzione, già l’anno scorso avevate organizzato il convegno Motori in corrente continua: aspetti funzionali e manutentivi (20 gennaio 2012, Confartigianato Vicenza), per ribadire come la tempistica dell’intervento sia fondamentale per evitare danni gravi alle macchine, lunghi fermo impianti e conseguenti perdite economiche per mancata produzione. Quali sono invece le novità che proponete quest’anno ai vostri clienti?
In vent’anni di attività, le piccole aziende come le grandi industrie – acciaierie, cartiere, aziende di stampaggio materie plastiche, aziende manifatturiere di tutti i settori – ci hanno sempre chiamato come si chiamano i medici del pronto soccorso dopo un incidente, e non per una semplice ferita da ricucire, ma sempre per resuscitare il cuore della macchina, ciò che dà vita all’intero ciclo produttivo. Sappiamo bene quale sia il valore del tempo per chi si rivolge a noi e, proprio per questo, abbiamo investito in tecnologia e formazione per dare ai nostri clienti la possibilità di prevenire, anziché curare, perché i costi della prevenzione sono di gran lunga inferiori a quelli dei danni provocati dalla malattia. Da quest’anno, i nostri tecnici, dotati di opportune strumentazioni (termocamere a infrarossi IR, vibrometri), sono in grado di effettuare analisi termografiche e vibrazionali degli impianti in funzionamento per il rilevamento di anomalie invisibili a occhio nudo, che consentono di evitare fermo macchine o, peggio, incendi. Spesso purtroppo si sottovalutano gli effetti di un incendio – distruzione di merci e macchinari, perdita di produzione, danni idrici, per non parlare della perdita di vite umane –, eppure, considerando che il 35 per cento di tutti gli incendi industriali sono causati da problemi elettrici, basta un’analisi predittiva come quella che sono in grado di eseguire i nostri tecnici per scongiurare tali tragiche eventualità.
Come funziona l’analisi termografica e qual è il suo valore aggiunto come strumento diagnostico?
Considerando che la radiazione termica si situa nella zona degli infrarossi, proprio come il calore della luce del sole o del fuoco, la termocamera IR consente di leggere i valori di temperatura trasformando un’immagine a infrarossi in un’immagine termica visibile e leggibile: ogni pixel nell’immagine che ci viene restituita sullo schermo della termocamera corrisponde a un’unità di misura della temperatura. I vantaggi di questo strumento diagnostico per un’azienda di produzione sono impagabili: oltre a far risparmiare tempo e denaro, aiuta a trovare le inefficienze prima che si trasformino in guasti, permette di effettuare ispezioni con sistemi sotto carico, dà un’immagine completa della situazione dell’impianto produttivo e, per di più, compie la sua indagine senza venire in contatto con i macchinari, quindi non è assolutamente invasiva.
Su quali tipi di impianti è possibile effettuare una termografia?
Un’immagine termica è in grado di dare rapidamente una panoramica di tutti gli impianti elettrici, meccanici e idraulici, evitando lunghi e laboriosi controlli dei singoli componenti uno alla volta.
Negli impianti elettrici, oltre a verificare lo stato di efficienza dei motori elettrici, può rilevare l’ossidazione degli interruttori, il surriscaldamento dei collegamenti, segnalando sovratemperature di qualsiasi dispositivo percorso da corrente elettrica.
Negli impianti meccanici, riesce a riscontrare un eventuale disallineamento dei giunti, l’usura degli ingranaggi dei riduttori, l’usura o la lubrificazione non corretta dei cuscinetti e lo stato di tutti gli elementi di scorrimento o rotolamento.
Negli impianti idraulici, analizza tutti gli organi d’intercettazione (per esempio, le valvole), scopre eventuali rotture, perdite di isolante e accumulo di sedimenti all’interno delle tubazioni, la corrosione subdola degli isolamenti termici, l’usura o la rottura di materiale refrattario nelle caldaie, nei forni e negli inceneritori e controlla il livello del liquido nei serbatoi e nei silos.
Come viene accolta la proposta di questo servizio innovativo da parte dei clienti?
Basti pensare che, da quando abbiamo incominciato a proporlo all’inizio di quest’anno, abbiamo avuto richieste per effettuare un’analisi praticamente tutti i giorni e i clienti sono rimasti soddisfatti perché abbiamo consentito loro di evitare il peggio.
Per fare qualche esempio tratto dalle nostre visite recenti, abbiamo rilevato problemi, che presto si sarebbero trasformati in danni, in varie parti degli impianti come circuiti di raffreddamento di bronzine scorrimento albero, collettori ad anelli di generatori sincroni, portafusibili con fusibili, connessioni di cavi in morsettiera, spazzole e relativi collegamenti, cuscinetti, turbine idroelettriche, giunti canali aria calda, canali di riscaldamento, caldaie, salvamotori, teleruttori, armadi elettrici, trasformatori MT, elettropompe e motori in genere.
I vostri tecnici sono in grado di effettuare anche analisi vibrazionali. Quali sono i vantaggi di questo esame?
I vantaggi dell’analisi vibrazionale sono gli stessi dell’indagine termografica: cambiano i parametri rilevati, non più legati alla temperatura, ma alle vibrazioni meccaniche. Infatti, ciascuna parte di un’attrezzatura con componenti rotanti ha un tipo di vibrazione che la caratterizza. Qualunque variazione di tale vibrazione può essere utilizzata per individuare, con precisione, la presenza di problemi quali usura dei cuscinetti, disassamento dei giunti meccanici, squilibrio o problemi elettrici al motore, usura di ingranaggi, di ventole, di cinghie, problemi al ventilatore, alle pale di una turbina o possibili combinazioni di tali problemi.
L’analisi delle vibrazioni è in grado di diagnosticare i problemi non appena diventano percettibili: dovrebbe essere eseguita periodicamente, in modo da “costruire” una linea di tendenza delle vibrazioni dell’attrezzatura ed evitare tempi di inattività e costi imprevisti.
E per il futuro, quali novità avete in cantiere?
Il prossimo passo sarà offrire ai clienti il controllo funzionale delle macchine elettriche rotanti da accesso remoto dalla nostra sede, in modo da sollevare la loro squadra manutentiva da questo importante quanto impegnativo e complesso compito operativo.